Just How Welding Evaluation Contributes to Longevity and Reliability in Manufacture Jobs
Welding evaluation offers as a fundamental element in making sure the long life and dependability of fabrication jobs. By methodically recognizing potential flaws throughout numerous stages of production, welding evaluations not just protect against costly failures however likewise cultivate a society of quality assurance within the team.

Relevance of Welding Inspection
Guaranteeing high quality with welding evaluation is an essential part of any kind of manufacture task. It functions as a secure to validate that welding procedures satisfy well established criteria and specifications, thereby boosting the general stability of the structure or component being fabricated. Welding inspection is not merely a procedural step; it is a necessary technique that assists determine potential issues early, making certain that they are resolved prior to they intensify into substantial troubles.
The value of welding evaluation can be underscored by its duty in keeping security and resilience. Welded joints are usually based on extreme problems, and any type of defects can endanger the performance and longevity of the last product. By applying extensive evaluation methods, organizations can ensure conformity with industry laws, thus minimizing dangers associated with architectural failures.
Additionally, effective welding examination promotes self-confidence among stakeholders, consisting of customers and regulative bodies, that the task satisfies the finest quality criteria. This not only boosts the reputation of the maker but likewise adds to long-term expense financial savings by staying clear of rework and potential obligations. Eventually, welding evaluation is important to the success and integrity of construction jobs, strengthening the value of high quality assurance in engineering methods.
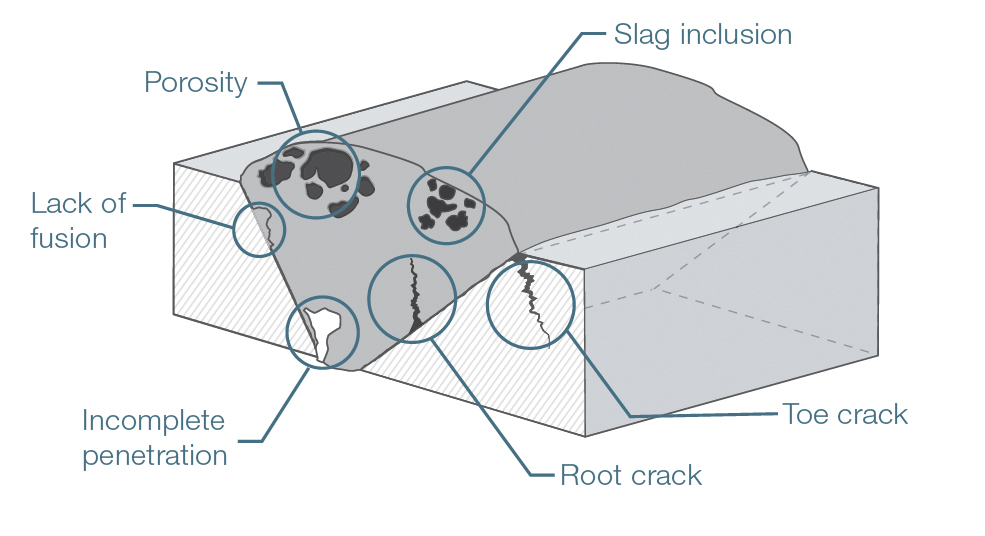
Common Welding Defects
Welding defects can considerably undermine the structural honesty of made parts, making their recognition and rectification important. Typical welding problems can be broadly classified right into 3 types: geometric, metallurgical, and service-related.
Geometric defects consist of problems such as undercutting, where the base steel is deteriorated at the side of the weld, and excessive convexity, which can lead to stress and anxiety focus points. These defects can endanger the stamina and sturdiness of the weld joint.
Metallurgical problems arise from inappropriate welding procedures or materials, bring about issues such as porosity, where gas pockets form within the weld, and absence of combination, which occurs when the weld steel fails to bond properly with the base steel. These issues can dramatically deteriorate the weld's effectiveness.
Service-related issues may not emerge until after the element is in usage. Instances include cracking because of thermal stress or exhaustion, which can result in disastrous failures if not addressed.
Comprehending these typical defects equips makers to implement reliable inspection methods that enhance the integrity and durability of their projects, eventually ensuring safety and security and performance standards are met.
Assessment Methods and techniques
An extensive approach to inspection methods and techniques is vital for determining and minimizing welding defects in construction jobs. Different techniques are employed to make certain the stability of welds, including aesthetic inspection, ultrasonic screening (UT), radiographic testing (RT), magnetic particle you can try this out testing (MT), and color penetrant screening (PT) Each strategy has its toughness and specific applications.

Magnetic fragment testing is helpful for spotting surface area and near-surface problems in ferromagnetic products. By using an electromagnetic field and making use of ferrous particles, examiners can identify interruptions efficiently. Color penetrant testing highlights surface-breaking problems via the application of a dye that seeps right into splits, making them visible under ultraviolet light.
Utilizing a mix of these approaches ensures an extensive evaluation, boosting the reliability of welded structures.
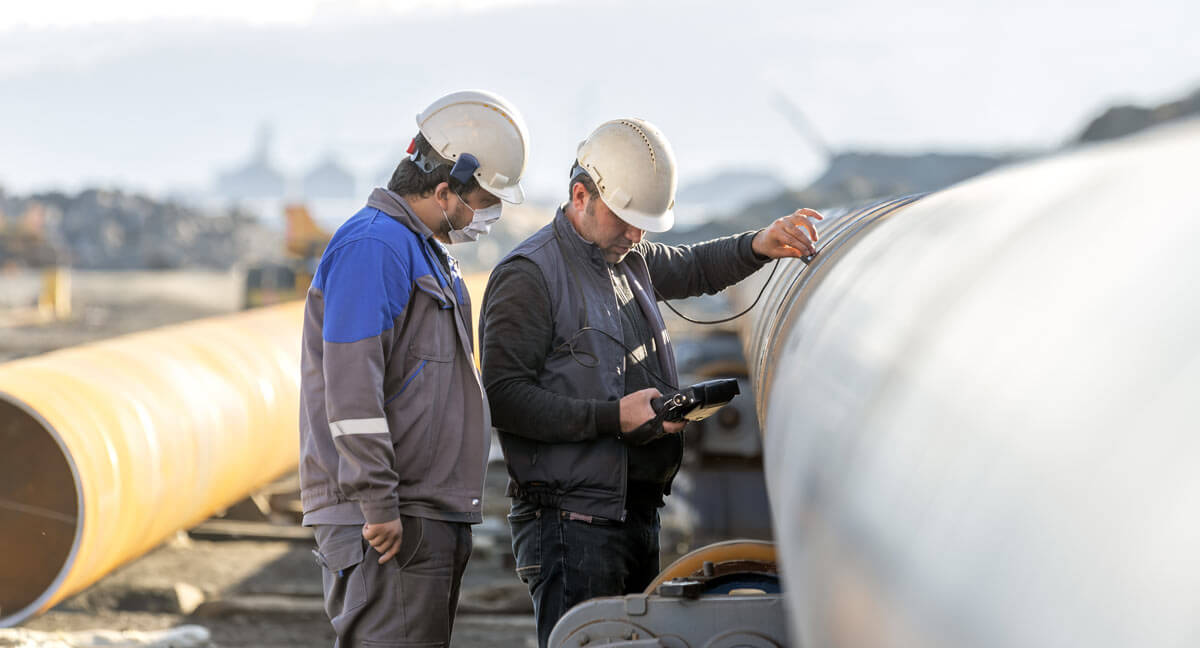
Effect On Project Long Life
Reliable assessment methods considerably influence the long life of manufacture jobs. By recognizing prospective flaws and incongruities in welding processes, evaluations guarantee that frameworks are built to hold up against functional tensions over time. When welds are extensively taken a look at, the probability of undiscovered concerns, which might result in architectural failures, is minimized.
Normal evaluations facilitate adherence to market standards and laws, which are important for making sure the resilience of bonded joints. Such compliance not just improves the honesty of the job but likewise reassures stakeholders relating to the quality of the job. Additionally, timely detection of flaws allows for rehabilitative activities to be taken early, stopping costly repair services or total overhauls down the line.
Additionally, efficient examination practices promote a society of quality control within construction groups. They are more likely to adhere to finest methods and maintain high criteria throughout the production process when employees are conscious that their work will be rigorously examined. Inevitably, this dedication to top quality not just expands the life-span of the project but also decreases maintenance expenses, thus improving the general economic feasibility of construction undertakings.
Enhancing Reliability in Fabrication
Integrity in manufacture is substantially improved through rigorous examination procedures that deal with potential weak points in welding methods. Efficient welding inspection not just determines problems early yet likewise offers critical responses to welders, making certain adherence to established specs and standards. By making use of non-destructive testing approaches, such as radiographic resource or ultrasonic evaluations, makers can establish the integrity of welds without endangering the material.
In addition, regular examinations promote a society of high quality and liability among manufacture teams. When welders recognize that their work undergoes strict analyses, they are most likely to comply with finest practices and procedures. This positive strategy reduces the risk of pricey failures throughout the operational phase of a job.
Furthermore, detailed paperwork of evaluation results produces an important database of details that can be used for future projects. Trends in defects can be assessed to enhance welding strategies and training programs (Welding Inspection Milwaukee). Eventually, boosting integrity in manufacture via comprehensive inspection processes not only raises the lifespan of the made elements however likewise enhances stakeholder self-confidence in the job's overall top quality and durability. Buying robust welding inspection techniques is important for accomplishing long-term integrity in any type of fabrication venture.
Verdict
In recap, welding assessment offers as a crucial part in guaranteeing the longevity and integrity of construction tasks. Inevitably, efficient welding evaluation methods strengthen stakeholder confidence and substantially contribute to the financial practicality of manufacture endeavors.
Welding evaluation serves as a fundamental aspect in my site making sure the long life and integrity of construction projects.Ensuring top quality through welding inspection is an important component of any construction job. Eventually, welding examination is essential to the success and integrity of manufacture projects, strengthening the value of quality assurance in design practices.
A detailed method to assessment strategies and approaches is vital for recognizing and minimizing welding defects in fabrication tasks.In recap, welding examination offers as a crucial element in guaranteeing the long life and reliability of fabrication jobs.